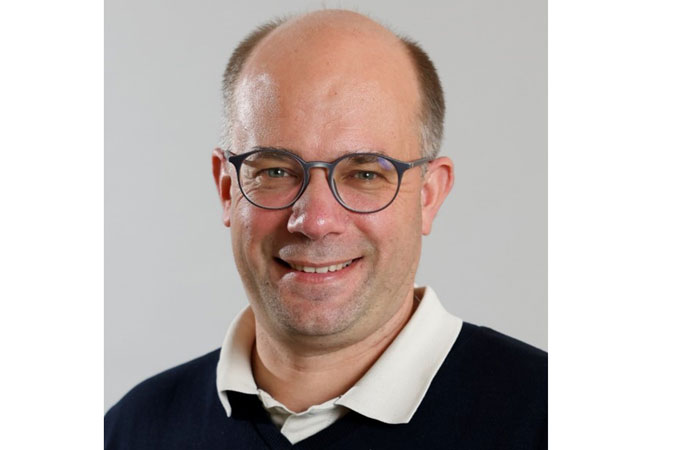
Stephan Pottel
Connected factory needs connected leaders
DUBAI, May 14, 2025
Stephan Pottel
Greater strategic alignment is needed among manufacturing executives to achieve digital transformation, suggests Zebra’s latest Manufacturing Vision Study.
It found that 38% of C-suite, 42% of IT, and 45% of OT leaders say they are the primary driver of factory workforce technology. While these leaders share many similar concerns across digitalisation, productivity, and labour, there needs to be clearer agreement about strategic ownership.
However, 67% of leaders in Europe say they don’t know how to start the process of digitally transforming the plant floor. Key barriers to digital transformation include identifying which business challenges or plant floor areas to start with, costs and availability of resources, and scalability of projects from pilot to organisation-wide implementation.
While 57% of manufacturing leaders globally (compared to 49% in Europe) expect to increase visibility across production and throughout the supply chain by 2029, one-third say getting IT and OT to agree on where to invest is a key barrier to digital transformation. Eighty-nine percent of leaders surveyed plan to increase technology and physical infrastructure investments, and 80% plan to increase their investment in staffing.
These are promising and ambitious investment plans, but without clear strategic alignment across leadership and knowing how to begin, resource, and scale projects, there could be a risk of money wasted and poor execution. This is why something like a connected factory framework is needed to support strategy and execution.
No AI in manufacturing without data
The study also shows that 54% of manufacturers in Europe (61% globally) expect AI to drive growth by 2029. This surge in AI adoption, combined with 92% of respondents prioritising digital transformation, underscores manufacturers’ intent to improve data management and leverage new technologies that enhance visibility and quality throughout the manufacturing process. In the next five years, decision-makers plan to drive process automation by implementing deep learning (63%) and machine learning (64%), while large language models (64%) and prescriptive workflows (59%) will be used to support decision automation.
A few months ago, the AI Summit in Paris powerfully shifted the tone around AI toward big investment, calculated risk taking, and the drive to win with the best AI development and real-life outcomes for business and society. It should provide another catalyst for manufacturing leaders to think more about their own AI investment strategy, even in the face of tough times, fluctuating demand and geopolitics.
The EU President, Ursula von der Leyen said: “European AI focuses on AI adoption in complex applications, using our unique industrial and manufacturing data and know-how,” which is true. The use cases and compliance requirements for pharmaceutical, automotive, electric battery, semiconductor and food makers are high and require more advanced AI such as deep learning and 3D scan software to handle them.
These AI ambitions are naturally tied to the need for data – lots of high value, good quality data, which we see in manufacturing across many processes. “Industries will be able to collaborate and federate their data. We are creating the safe space for them…because AI needs competition but also collaboration,” said President von der Leyen.
The volume of data being created at the edge of business can be turned into value. That could be data for training and testing machine vision deep learning models or acting as feedback to refine visual inspection processes. Once data and AI are integrated, the path to intelligent automation – with smart cameras, sensors, and vision-guided robotics – becomes a reality, allowing leaders to reallocate valuable frontline workers to growth-focused areas.
However, manufacturing sites and regions can operate in silos, with little to no sharing of data, even for identical or similar workflows. Experience and time available can vary between teams and sites which can make achieving data quality more challenging, compounded by struggling to hire the right talent with the right skills and experience. Data needs to be stored, annotated, and shared, and duplicate, obsolete and inaccurate data removed. Then it’s ready for things like AI model training and testing.
Manufacturers can achieve a truly connected factory if they learn to leverage all the data available to them across workflows, sites, countries, and regions, to fuel growth and workforce productivity.
New tooling for workers and workflows
When it comes to strategic execution, the study finds that manufacturers are shifting their growth strategies by integrating and augmenting workers with AI and other technologies to transform manufacturing and build a skilled workforce over the next five years.
Seventy-one percent of manufacturing leaders plan to reskill labour to enhance data and technology usage skills, and seven in 10 (62%) expect to augment workers with mobility-enabling technology. They also rank ongoing development (61%), retraining/upskilling (66%), and career path development (63%) as high priorities to attract future talent.
The technology tools being implemented by manufacturing leaders for their workers include tablets (54%), mobile computers (54%), and workforce management software (57%). In addition, 61% of manufacturing leaders plan to leverage wearable mobile computers to augment their evolving workforce. But leaders across the C-Suite, IT and OT understand how labour initiatives must extend beyond improving worker efficiency and productivity with technology.
Most manufacturing leaders agree that technology investments in intelligent automation solutions are driven by a variety of factors including the need to provide the workforce with high-value tasks (69%), achieve service level agreements (69%), and add more flexibility to the plant floor (63%). And they’re looking to robotics (63%), machine vision (66%), radio frequency identification (RFID) (62%), and fixed industrial scanners (53%) to turn driving factors into growth levers.
Manufacturers want to make smart, connected factories a reality, equipped with modern systems that drive connections across the plant and promise unprecedented asset visibility, efficiency and flexibility. High quality, connected data fueling AI systems, truly real-time insights, and people better connected to each other, data, and systems is the future.
Toward the connected factory – real life examples
• TAS, the OEM supplier of electric battery caps to luxury car makers secured increased and consistent product quality, with a reliable and precise vision-guided robotics solution using Zebra’s Aurora Vision Studio machine vision software with deep learning.
• Pollini, an automotive parts reseller and recycler processing 70-80 end-of-life vehicles daily and maintaining stock of around 350,000 items reduced device workflow disruptions by 20% and improved device resolution times by 10% using Zebra rugged devices and VisiblityIQ Foresight predictive maintenance software using machine learning.
• Zeelandia is a leading bakery solutions provider to industrial and mid-size bakeries is saving at least €20,000 annually, thanks to a Zebra wireless fixed industrial scanning solution.
• Marexi, a marine food manufacturer is achieving visual inspection rates approaching 100% accuracy, with a system that can now process up to 20 tons of frozen tuna per hour by species, size and quality, using with Zebra’s AltiZ high fidelity 3D profile sensor technology.
• I.D.E.A, an industrial automation provider for the automotive industry can inspect 200 different brake discs with a single machine vision system built on Zebra’s Aurora Design Assistant™ software. The new, rapid system delivers enhanced quality control, inspections are repeatable 24 hours a day, and the user interface is easy to use.
• An industrial bakery inspects its full range of breads using a single machine vision solution, and carry out efficient, automated picking with a robotic grip handling between 25 and 30 packages per minute without damaging bread or packaging. Estimated 75% cost saving using Zebra’s Aurora Design Assistant machine vision software.
• Bidfood: large paper and packaging manufacturer implemented a fleet of handheld and vehicle-mounted rugged devices and Zebra Cloud DNA software tools, for secure device management, frontline worker self-serve options, and efficient operational workflows. – TradeArabia News Service
*The writer, Stephen Pottel, is the Manufacturing Strategy Director, EMEA, Zebra Technologies